KMB punches parts into precise shapes
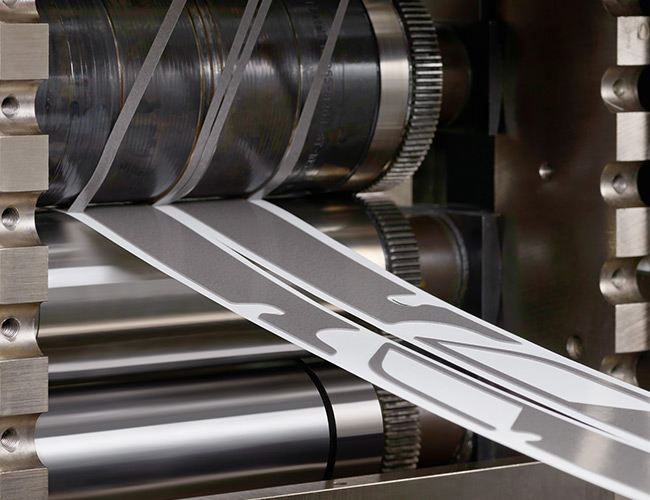
KMB manufactures punched parts from adhesive and non-adhesive materials. We produce from roll to roll, from sheet to sheet, from roll to sheet or individual punched parts. We manufacture parts with the highest precision for you in the following formats:
- Roll punching formats up to 550 mm wide and 1200 mm long
This allows us to produce individual punched parts, punched parts on rolls or cut roll goods of all common sizes for a variety of purposes. We manufacture punched parts from various carrier materials and can include pull-off aids (e.g. finger lifts) if desired. Fabric adhesive tapes, punched parts with foam backing, felts, foils, acrylic foams or VHB adhesive tapes – we use modern technology to give you the exact shape you need. The bonding specialists at KMB are also happy to take on special challenges, such as producing punched parts from difficult to process materials. If necessary, we also develop our own procedures for this purpose.
Tool-less punching
In addition to the "classic" process in which a punching tool is used, KMB has also offered the technical requirements for tool-less punching since 2008. The possible applications of this process, which is based on modern laser technology, are versatile and often more cost-effective for small runs.
Prototypes can also be produced thanks to modern laser technology. If the nature of the material doesn’t allow this, we can alternatively produce prototypes using our cutting plotter. Just tell us what you need.
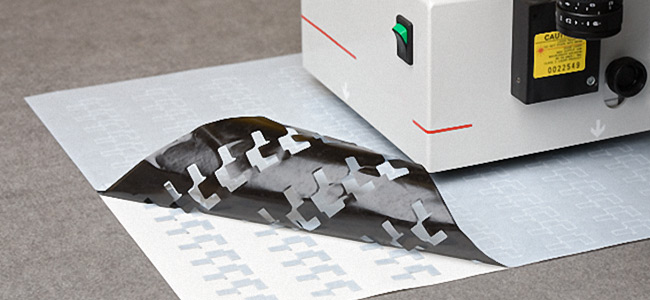
Real-life examples
Our goal is to offer you solutions that exactly meet your requirements time and time again – whether it’s for a small run or for series production. Here are some examples which KMB were responsible for from development to production.
Sector: Electronics industry
The task:
An American company required precisely maintained hole punching at precisely defined intervals for further machine processing.
The solution:
KMB developed a production process that punches the millimetre-sized holes in the exact position intended. This resulted in the number of rejects during mechanical processing being reduced considerably.
The result:
Perfectly calibrated hole punching saves production costs and reduces problems during subsequent processing.
Sector: Automotive industry
The task:
The material butyl was to be used as a seal in the automotive industry and had to be punched hole-in-hole. In addition, the sealing rings were very small and the sealant butyl sticks quickly to the stamping die mould and is therefore difficult to process.
The solution:
KMB uses a production process that allows butyl to be processed precisely and quickly despite the small distance between the inner and outer hole.
The result:
The client's specifications were met 100% despite the challenges presented by the material.
Sector: Various
The task:
The backing paper should be easier to remove from the adhesive using tabs.
The solution:
Depending on the area of application or subsequent processing, KMB offers various possibilities for integrating so-called finger lifts. During the punching process, a flap can be integrated in addition to the original shape, or the length or width of the original format can be extended by a finger lift.
The result:
Less waste during processing and easier removal from the carrier material, thus saving costs.
Sector: Various
The task:
The supplier of a processing company was delayed in delivery due to technical problems.
The solution:
KMB took over the project and produced 190,000 double-sided adhesive labels at short notice using the raw material supplied by the customer. A particular challenge here was the exposed adhesive surface.
The result:
Thanks to KMB's flexibility, the supplier was able to fulfil its obligations to its client on schedule.
Sector: Injection moulding and automotive industry
The task:
A supplier to the automotive industry produces chrome-plated plastic lettering. These injection moulded parts are then furnished with a self-adhesive finish for easy final assembly in the factory.
The solution:
KMB produced double-sided adhesive punched acrylic foam parts that make the lettering and bodywork a robust unit. The parts were delivered on rolls for cost-saving machine processing purposes. Precisely punched pilot holes on the carrier material and recesses on the adhesive surface allow for precise mounting.
The result:
KMB supplies solutions which are thought through to the last detail and which help optimise the workflow.
See the other services der KMB Klebetechnik GmbH offers.